PROCESSING APPLICATION
Hold tight! We’re comparing your resume to the job requirements…
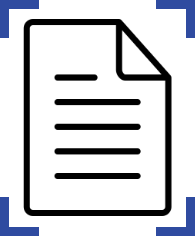
ARE YOU SURE YOU WANT TO APPLY TO THIS JOB?
Based on your Resume, it doesn't look like you meet the requirements from the employer. You can still apply if you think you’re a fit.
Job Requirements of Maintenance Team Leader - Night Shift:
-
Employment Type:
Full-Time
-
Location:
Hopkinsville, KY (Onsite)
Do you meet the requirements for this job?
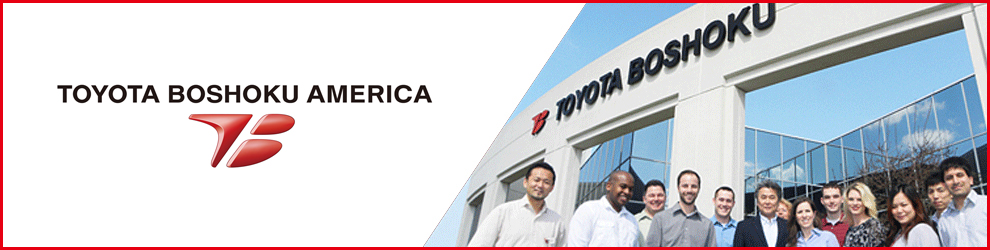
Maintenance Team Leader - Night Shift
Available Openings - 1 on 2nd shift
$30.15/hr. starting (+$1.50/hr. for 2nd shift) -- increases every 6 months to maximum of $37.25.00/hour within three years.
I. General Summary
Directs Team Members in assigned manufacturing area(s) in the execution of the team leader responsibilities. Support the manufacturing areas and maintain the overall Toyota Production System with a focus on minimizing down time, increasing productivity, and coordinating preventative maintenance activities. Assigns tasks as an operational unit and responsible to accomplish company goals and targets in accordance with all company policies, maintenance standards and methods, and standards for safety, quality, productivity, cost reduction, housekeeping, efficiency, training, teamwork, and morale.
II. Essential Job Functions:
General
A. Functions as a team leader with team members.
1. Understand, execute, and ensure consistent compliance with all company rules, policies, and practices in accordance with the terms of the Team Member Handbook.
2. Develop and maintain positive team member relations centered on mutual trust, dignity, respect, fairness, consistency, two-way communication, teamwork, and harmony.
3. Provide direction and motivation to team members emphasizing safety, quality, efficiency, productivity, cost reduction, and morale.
B. Responsible for leading and maintaining the maintenance and repair operations.
1. Develop standardized work procedures by designing and/or documenting the best maintenance work sequence for each piece of equipment or tooling.
2. Assign the work of team members by assigning/re-assigning work stationing based on current work situation and production schedules.
3. Assign floor activities through consistent application of Toyota Boshoku Business Practices (TBBP) to ensure all aspects of manufacturing maintenance and repair operations are effective and correct sub-standard situations.
4. Perform the essential job functions of team members as necessary to maintain efficient, stable, and continuous operations.
C. Assign and support maintenance activities on all production equipment, facilities, and utility systems to provide a reliable production platform.
1. Assign and support activities of team members engaged in repair, maintenance, and installation of machines, tools, and equipment to ensure continuous production operations.
D. Utilize knowledge and skills to maintain the highest level of safety and efficiency for machines, tools, equipment, etc. possible.
1. Partner with the Manufacturing department to initiate investigation and containment activities.
2. Troubleshoot daily safety, machine, equipment, and tooling issues.
3. Be proactive in predicting abnormalities and finding innovative solutions to correct.
4. Evaluate and analyze problems involving machinery and equipment and coordinates repair of tools and machinery. Participate in frequent evaluation of machines, tools, equipment, etc.
E. Maintain a safe working environment for all team members.
1. Ensure compliance with safety regulations, PPE requirements, and company safety policies and procedures.
2. Lead, perform, and/or participate in 5S housekeeping, accident investigation, and safety audits and related activities.
3. Maintain knowledge of procedures concerning Hazardous Waste, Spill Response, and Plant Security.
4. Monitor safety and health of team members to ensure their well-being.
F. Train and coach team members, in performance, setups, trouble shooting, continuous improvement, and maintenance and repair operations.
1. Provide multi-skills training to effectively handle breakdown situations.
2. Support further development of team members through, feedback, coaching, and cascade training.
G. Communicate frequently with internal contacts on various issues.
1. Through daily communication meetings, keep team members informed on issues relevant to them and encourage two-way communication.
2. Maintain daily and/or frequent communication with upstream and downstream groups/areas and support departments to ensure efficient and stable operations in a team-based environment.
3. Coordinate communications between shifts for assigned area(s).
III. Minimum Qualifications/Requirements:
Education:
• High school diploma, GED, or equivalent required.
• Associate’s degree in Maintenance, Industrial Technology, or related field preferred.
• Skilled Trades journeymen status or certification from trade school, technical college, or apprenticeship preferred.
Experience:
• Minimum three (3) years of relevant maintenance experience required.
• Experience in maintenance and repair operations associated with electrical systems, electronics, fabrication, hydraulics, injection molding, mechanical drives, pneumatics, robotics, stamping, welding, assembly and conveyor systems, and Programmable Logic Controller (PLC) programming and troubleshooting.
• Minimum two (2) years of leadership or supervisory experience preferred.
• Automotive industry experience preferred.
• Experience in automotive interiors including carpets, filters, powertrain, seating, and/or trim preferred.
• Working knowledge and experience with the Toyota Production System preferred.
Personal/Technical Skills:
• Demonstrated knowledge, skills, and abilities to perform the job functions of a leadership role.
• Ability to troubleshoot and track equipment issues to perform root cause analysis and correct issues with equipment suppliers.
• Must have a good working knowledge of industrial technology.
• General understanding and working knowledge of skill areas including electrical, electronics, fabrication, hydraulics, injection molding, mechanical drives, pneumatics, robotics, stamping, welding, assembly and conveyor systems, and PLC programming.
• Must be able to work in a multi-skilled environment with maintenance aptitude to learn skilled trades other than area of expertise.
• Ability to read and interpret blue prints, schematics, drawings, specifications, and technical instruction manuals.
• Thorough understanding of company product, trade terminology, maintenance and repair operations, manufacturing processes, and machine/equipment operation.
• General understanding and working knowledge of manufacturing and assembly equipment and tooling including design, automation, robotics, or manufacturing processes (and all secondary related processes) relating to automotive interiors.
• Working knowledge of shop mathematics and the use of a variety of measuring devices and instruments.
• Ability to effectively facilitate problem solving and resolution.
• Ability work with a dynamic team and demanding customer(s).
• Ability to work in a fast-paced, multicultural work environment.
• Ability to work with multiple departments and prioritize activities.
• Ability to plan, direct, assigns and performs functions of assigned areas.
• Ability to maintain on call flexibility to control abnormal conditions.
• Ability to be flexible in a constantly changing production environment.
• Active listener with effective leadership, communication, and interpersonal skills.
• Ability to diagnose problems for true root cause and implement effective countermeasures.
• Must be able to work a fixed or rotating shift schedule, including daily or weekend overtime.
• Must be able to multi-task, handle diversity, and provide leadership through problem resolution.
• Ability to communicate and work well with all levels of the organization in a team environment.
• Ability to adapt available skills and equipment to respond to unforeseen demands and/or problems.
• Ability to implement plans to control and maintain safety, quality, 5S, cost, and efficiency for assigned areas.
• Strong organization, time management, and planning skills and ability to manage multiple tasks with tight deadlines.
Language Skills:
• Strong verbal and written communication skills in English.
Computer/Software:
• Previous experience working with integrated computer programs and/or applications. ERP System experience (e.g., Oracle) preferred.
• Solid working knowledge and demonstrated experience with Microsoft Office and other computer-based applications (e.g., MS Word, MS Excel, MS PowerPoint, Outlook, Internet, etc.).
Training Requirements:
Must be willing to successfully complete and use training for items below:
• Machines, tools, tooling, equipment, and other motorized or maintenance related equipment (e.g., cranes, lift trucks, etc.).
• Cross training for leading other plant support departments.
• RCRA and DOT hazardous waste requirements, and pass certification.
• Computer-based software, applications, and systems (e.g., Oracle, Kronos, Future 3, etc.).
IV. Work Environment/Conditions:
Office: Open Office Environment, moderate noise level.
Plant: Various types of manufacturing environments.
• Standard automotive plant environment with moderate noise level.
• PPE (Personal Protective Equipment) such as safety glasses, steel toe shoes, Kevlar sleeves, hearing protection, etc. may be required in designated engineering, manufacturing, or industrial areas. Personal attire standards may apply.
• Involves moderate or occasional presence of some slightly disagreeable conditions, i.e., cold, dust, heat, odor, etc.
Travel: Minimal (Able to travel to Japan for training and benchmark activities-Able to travel to other TBA facilities for training and benchmark activities.)
V. Physical Demands:
While performing the duties of this job, the team member is required to talk, hear, and see (with visual acuity). Performance requires mental alertness and sustained attention to needs of the department in terms of workflow, efficiency of operation, machine adjustment, and team member output. Performance requires physical ability to inspect, adjust, and operate equipment. The team member must be capable of walking, sitting, and standing for extended periods of time throughout plant. Occasionally climbing, stooping, or bending on, under, or near tooling and equipment. May be occasionally required to reach, grasp, and manipulate parts, materials, or equipment. May be occasionally required to lift up to 30-50 pounds (with or without assistance).