PROCESSING APPLICATION
Hold tight! We’re comparing your resume to the job requirements…
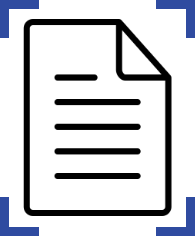
ARE YOU SURE YOU WANT TO APPLY TO THIS JOB?
Based on your Resume, it doesn't look like you meet the requirements from the employer. You can still apply if you think you’re a fit.
Job Requirements of Senior Production Engineer:
-
Employment Type:
Full-Time
-
Location:
CAN (Onsite)
Do you meet the requirements for this job?
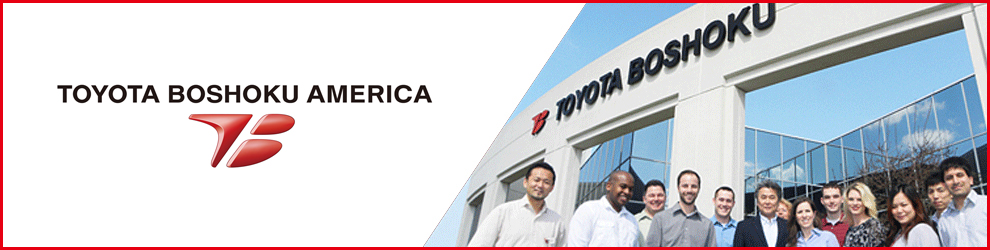
Senior Production Engineer
I. General Summary: Utilize the Toyota Production System and engineering skills to perform Production Engineering functions to establish and setup for seat assembly processes within Tier 1 automotive manufacturing plants. Responsible to provide technical support and monitoring processes to ensure that team objectives are met with regard to delivery of quality parts on time to the customer. Plan, source, manage, and install new in-house seat assembly projects on time and on budget.
II. Essential Job Functions:
A. Develop and implement process and production preparation plans for new seat assembly automotive tools, equipment, and products.
1. Conduct research to develop and test new fabrication processes and procedures.
2. Develop new or modify current seat assembly methods, techniques, and procedures.
3. Establish assembly instructions/visual aids to guide production team relating to specifications/processes.
4. Evaluate new developments in the automation field for possible application to current seat assembly problems or production processes.
5. Assist in development and maintenance of work instructions in compliance with TS16949 requirements.
6. Set up automation processes, train manufacturing staff, and hand over completed process to manufacturing teams.
7. Coordinate technical personnel in performing inspections to ensure worker’s compliance with established seat assembly procedures, restrictions, and standards.
8. Communicate project status to other departments and manufacturing plants.
9. Support plant manufacturing and engineering staff during new program launches.
B. Manage tool and equipment sourcing.
1. Lead or assist with supplier selection process including project quotations and Requests for Quotation (RFQ).
2. Create and manage purchase orders for tools and equipment.
3. Manage suppliers in the design, construction, and installation of new tools and equipment.
C. Improve existing or develop new equipment and tooling including managing Engineering Change Instructions (ECI).
1. Perform experimental assembly to evaluate new equipment, techniques, and materials.
2. Actively contribute to the machine design from the manufacturing engineer’s perspective and liaise with other engineers in the team during the design and manufacturing process to ensure that the manufacturing process requirements are adhered to.
3. Assist with writing equipment specifications for new or modified equipment and/or obtaining agreement on specifications of equipment from plants and other departments.
4. Manage all ECIs for tooling and equipment including supporting equipment and tooling work.
D. Prepares technical reports as a result of research, development, and preventative maintenance investigations.
E. Initiate action to prevent the occurrence/reoccurrence of any nonconformities relating to product, process, and quality system.
1. Conduct root cause analysis and problem solving methods.
2. Interface with internal/external customers and lead team members in problem solving with regard to production, customer, and supplier concerns.
F. Create and manage project budgets and associated paperwork and recordkeeping related to projects, schedules, Ringi documents, ECIs, drawings, data, etc.
III. Minimum Qualifications/Requirements:
Education:
• Bachelor’s degree in Manufacturing, Mechanical Engineering, or related technical field required.
Experience:
• Greater than four (4) years of relevant experience required.
• Manufacturing experience in general assembly, automation, ultrasonic welding, screw tightening, vacuum forming, edge folding, ornament lamination, etc.
• Equipment procurement experience.
• Two or more years of experience in automotive manufacturing engineering preferred.
• Experience in automotive interior components (e.g., injection, assembly, tooling, and other miscellaneous components), managing projects from design to production, is preferred.
• Experience in automotive seating related processes is preferred.
Personal/Technical Skills:
• Ability to order and track equipment and material for the manufacturing facilities.
• Working knowledge of tool and equipment design, automation, robotics, and/or manufacturing processes.
• Basic understanding of the industrial equipment and manufacturing processes relating to automotive interiors.
• Ability to troubleshoot and track equipment issues to perform root cause analysis and correct issues with equipment suppliers.
• Basic knowledge of cost structures and/or Process Failure Mode and Effects Analysis (PFMEA) development is preferable.
• Ability to read component, assembly and equipment drawings and have an understanding of Geometric Dimensioning and Tolerancing (GD&T).
• Effective time management skills.
• Ability to work in a team environment.
• Ability to adopt a self-directed work style.
• Strong organization, planning, and analytical skills.
• Ability to compile effective and concise visual reports.
• Able to work in a fast paced, multicultural work environment.
• Familiar with root cause analysis and problem solving methods.
• Active listener with effective communication and interpersonal skills.
• Ability to multitask, manage diversity, and facilitate problem solving and resolution.
• Ability to function both independently and with good judgment in a team environment.
• Ability to communicate and work well with all levels inside and outside of the organization.
• Must be able to work flexible hours to support production on all shifts during new product launch.
• Ability to collect and organize data in an orderly fashion so that it can be accessed and use for future programs.
• Must be able to compile information and report that information to the appropriate people in the organization in a timely manner.
Language Skills:
• Strong verbal and written communication skills in English.
• Japanese, Spanish, and/or Portuguese would be helpful.
Computer/Software:
• Solid working knowledge and demonstrated experience with Microsoft Office and other computer-based applications (e.g., MS Word, MS PowerPoint, MS Project, Lotus Notes/Outlook, Internet, etc.).
• Must be proficient in MS Excel, AutoCAD, and 3D Modeling software.
• CATIA experience is preferred.
• PLC experience is a plus.
• Experience with MS Access is preferred.
IV. Work Environment/Conditions:
Office: Open Office Environment, moderate noise level while performing manufacturing automotive production engineering operations.
Plant: Standard automotive plant environment with moderate noise level. PPE (Personal Protective Equipment) such as safety glasses, steel toe shoes, hearing protection, etc. may be required in engineering, manufacturing, or industrial areas. Personal attire standards may apply.
Travel: Up to 50% travel required at times to our vendors and plants (Mississippi, Indiana, Michigan, Kentucky, Canada, Argentina, Brazil, and Japan).
V. Physical Demands: Ability to sit and work on a computer for extensive periods of time is required. While performing the duties of this job, the team member is required to talk, see, and hear. Performance requires physical ability to inspect, adjust, and operate equipment. The team member must be capable of walking, sitting, and standing for extended periods of time throughout plant. Occasionally climbing, stooping, or bending on, under, or near tooling and equipment. May be occasionally required to reach, grasp, and manipulate parts, materials, or equipment. May be occasionally required to lift up to 30-50 pounds (with or without assistance).
Disclaimer: This job description is intended to identify the general nature and level of work performed by team members within this classification, as well as certain essential job functions. It is not intended, and should not be interpreted, as a comprehensive inventory of all duties, responsibilities, and qualifications required of team members assigned to this job. To qualify for this job, however, a team member must be able to perform its essential functions with or without reasonable accommodation. Under no circumstances may this job description be construed as altering the at-will nature of the employment relationship between TBA and any team member.
EOE