PROCESSING APPLICATION
Hold tight! We’re comparing your resume to the job requirements…
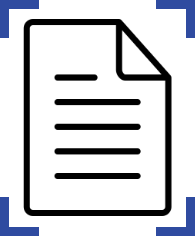
ARE YOU SURE YOU WANT TO APPLY TO THIS JOB?
Based on your Resume, it doesn't look like you meet the requirements from the employer. You can still apply if you think you’re a fit.
Job Requirements of Quality Specialist (Document Control):
-
Employment Type:
Full-Time
-
Location:
Mantachie, MS (Onsite)
Do you meet the requirements for this job?
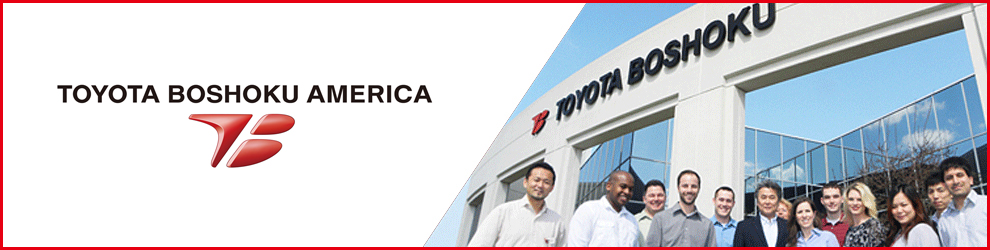
Quality Specialist (Document Control)
I. General Summary: To plan, develop, implement quality systems to ensure plant parts meet or exceed customer expectations. Coordinate maintenance and support the Process Owners in the deployment the manufacturing site’s Quality Management System to meet IATF 16949 applicable requirements. This role will coordinate, maintain and conduct internal audits to the automotive standard and develop internal auditors.
II. Essential Job Functions:
A. Coordinates the Manufacturing Site process owners’ efforts to meet the automotive standard requirements (ISO + IATF).
B. Promotes, develops and implements quality assurance procedures supporting process owners and systems to improve and maintain quality under the IATF 16949 automotive standards.
C. Ensures that all site employees are thoroughly familiar with the philosophy, quality statement, quality manual and are trained in the appropriate procedures under IATF 16949.
D. Supports in customer and internal quality audits. (ISO, IATF).
E. Coordinates and represents the site to maintain quality certifications (ISO, IATF).
F. Knowledge of and complies with all the applicable corporate, as well as site, laboratory policies/procedures with regard to Quality, personal conduct and safety.
G. Complete miscellaneous reporting, administrative, and other quality related functions for the Quality Control department as required including QC Circle participation, Key Performance Indicator (KPI) reporting, etc.
III. Minimum Qualifications/Requirements:
Education:
• Bachelor’s degree in Business, Engineering, or related field required; or an equivalent combination of education and relevant experience.
• Expert level knowledge of IATF 16949.
• Additional trade education and Quality certifications are preferred.
Experience:
• Greater than four (4) years of relevant manufacturing quality experience required, preferably automotive.
• 3 years minimum Quality Management systems experience in automotive industry. Preferably experience with Automotive OEM or suppliers
• IATF 16949/ISO 9001: 2015 Certified Auditor (Lead Auditor is a plus).
• Experience with manufacturing processes and quality control methods.
• Familiar with PFMEAs, Process Control Plans, Process Flow Diagrams, APQP, SPC and other quality documents.
• Proven successful track record in leading management system applications.
• Previous exposure to a multicultural office environment preferred.
Personal/Technical Skills:
• Working knowledge of quality audit techniques.
• Basic shop math ability required (i.e., addition, subtraction, multiplication, division).
• Understanding of conceptual math (i.e., basic geometry, charts and graphs) required.
• Understanding of elementary statistical concepts (i.e., standard deviation, variance, etc.).
• General understanding and working knowledge of product design specifications functions and quality standards of finished product as well as parts/materials used.
• Thorough understanding and working knowledge of automotive plants and processes, company products, trade terminology, quality management and control systems and techniques and manufacturing processes.
• General understanding of the Toyota Supplier Quality Assurance Manual (SQAM) and Toyota Production System (TPS) is preferred.
• Good understanding of seat, welding, door, carpet, and headliner processes are a plus.
• Good presentation skills.
• Effective time management skills.
• Ability to build work relationships amongst all teams, international and domestic
• Strong organization and planning skills.
• Excellent critical thinking skills required.
• Good assertiveness and negotiation skills.
• Ability to understand inspection standards.
• Hands-on, self-starter with a strong work ethic.
• Active listener with effective communication skills.
• Ability to compile effective and concise visual reports.
• Ability to perform responsibilities with minimal supervision.
• Ability to work in a fast-paced, multicultural work environment.
• Ability to maintain records and files and prepare recaps and reports.
• Ability to be flexible in a constantly changing production environment.
• Ability to communicate and work well with all levels of the organization.
• Ability to create excellent working relationships with internal and external customers.
• Must be able to work a fixed or rotating shift schedule, including daily or weekend overtime.
• Ability to multitask, manage diversity and facilitate effective problem solving and resolution.
Language Skills:
• Strong verbal and written communication skills in English.
• Japanese is a plus.
Computer/Software:
• Solid working knowledge and experience with Microsoft Office and other computer-based applications (e.g., MS Word, MS Excel, MS PowerPoint, Outlook, Internet, Newton, NEC, etc.).
IV. Work Environment/Conditions:
Office: Open Office Environment, moderate noise level.
Plant: Standard automotive plant environment with moderate noise level. PPE (Personal Protective Equipment) such as safety glasses, steel toe shoes, hearing protection, etc. may be required in engineering, manufacturing, or industrial areas. Personal attire standards may apply.
Travel: Must be willing to travel up to 10% of the time to TBA plants.
V. Physical Demands: Ability to sit and work on a computer for extensive periods of time is required. While performing the duties of this job, the team member is required to talk, see, and hear. The team member must be capable of walking, sitting, and standing for extended periods of time. May be occasionally required to lift up to 30 pounds.
Disclaimer: This job description is intended to identify the general nature and level of work performed by team members within this classification, as well as certain essential job functions. It is not intended, and should not be interpreted, as a comprehensive inventory of all duties, responsibilities, and qualifications required of team members assigned to this job. To qualify for this job, however, a team member must be able to perform its essential functions with or without reasonable accommodation. Under no circumstances may this job description be construed as altering the at-will nature of the employment relationship between TBA and any team member.
EOE