PROCESSING APPLICATION
Hold tight! We’re comparing your resume to the job requirements…
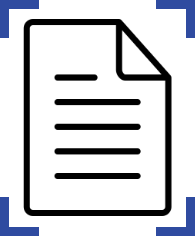
ARE YOU SURE YOU WANT TO APPLY TO THIS JOB?
Based on your Resume, it doesn't look like you meet the requirements from the employer. You can still apply if you think you’re a fit.
Job Requirements of Maintenance Facilities Team Leader:
-
Employment Type:
Full-Time
-
Location:
Jackson, TN (Onsite)
Do you meet the requirements for this job?
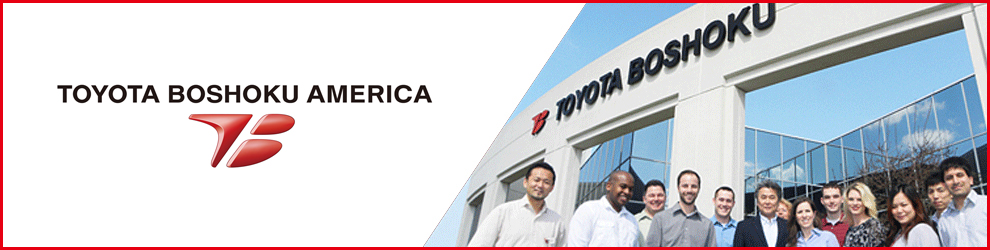
Maintenance Facilities Team Leader
Maintenance Facilities Team Leader
I. General Summary: Directs Facility Team Members in assigned manufacturing area(s) in the execution of the team leader responsibilities. Assigns tasks as an operational unit and responsible to accomplish company goals and targets in accordance with all company policies, maintenance standards and methods, and standards for safety, quality, productivity, cost reduction, housekeeping, efficiency, training, teamwork, and morale. Troubleshoot, repair, and maintain facility equipment utilizing mechanical, electrical, pneumatic, and hydraulic skills. Additional responsibilities include general maintenance and minor repair of the facility. As with all TBDN Associates, a Maintenance Facilities Team Leader is responsible for supporting the company’s mission statement and overall business objects by quality philosophy, following the environmental policy, and actively working to improve production results.
II. Essential Job Functions:
A. Determines, implements, and performs maintenance for facility equipment based on OSHA and company standards. B. Performance of all tasks in a manner which constantly meets or exceeds Standard Performance Levels. C. Adheres to all TBDN TENNESSEE COMPANY policies, procedures, and standards. D. Actively participates/supports the companies 5S program. E. Performs regularly scheduled PM on a wide variety of facility equipment. F. Installs, relocates, and modifies a wide variety of facility equipment. G. Performs routine checks and inspections on a wide variety of facility equipment. H. Responds to request from various sources to install/repair a wide variety item in the facility. I. Provides training, leadership, and guidance to facilities Team Members. J. Works with Engineering, Operations, and any other departments to effectively manage and complete tasks and projects. K. Make requests for any necessary parts equipment and tools. L. Maintains tools and work area in a clean and professional manner. M. Maintains the proper documentation and record keeping. N. Willingly performs any other duties that may be requested or assigned. O. Maintenance and preventative maintenance techniques. P. Read and interpret blueprints, equipment manuals, schematics and drawings. Q. Maintain knowledge of procedures concerning Hazardous Waste, Spill Response, and Plant Security. R. Monitor safety and health of team members to ensure their well-being. S. Train and coach team members, in performance, setups, trouble shooting, continuous improvement, and maintenance and repair operations. T. Provide multi-skills training to effectively handle breakdown situations. U. Support further development of Facility team members through, feedback, coaching, and cascade training. V. Communicate frequently with external vendors on various facility issues (Cranes,Air Compressors, etc). W. Through daily communication meetings, keep team members informed on issues relevant to them and encourage two-way communication. X. Follow safety, quality, confidentiality, and information security policies and procedures.
III. Minimum Qualifications/Requirements:
Education:
• Associates of Science in Engineering or Diploma from technical field required, or equivalent combination of education and relevant experience.
• Tradesman or Certified HVAC Technician preferred
Experience:
• Greater than two (2) years of Manufacturing Engineering or Maintenance experience required
Personal/Technical Skills:
• General manufacturing and industrial equipment knowledge required.
• General understanding and working knowledge of skill areas including electrical, electronics, fabrication, hydraulics, mechanical drives, pneumatics, welding, assembly, conveyor systems, and motors and pumps.
• Strong organization and planning skills.
• Must be able to effectively communicate both verbally and in writing technical data and operations information.
• Effective time management skills.
• Ability to perform responsibilities with minimal supervision.
• Kaizen mind.
• In depth troubleshooting skills.
• Licensed on lift trucks.
• Ability to communicate and document procedures and maintain records and logs.
• Basic machine shop skills
• Working knowledge of testing equipment and testing/analysis procedures.
• Able to follow all pertinent regulations, standards, and safety and environmental procedures.
Language Skills:
• Strong verbal and written communication skills in English.
Computer/Software:
• Working knowledge and experience with Microsoft Office and other computer-based applications (e.g., MS Word, MS Excel, MS PowerPoint, Outlook, Internet, etc.)..
• Previous experience working with integrated computer programs and/or applications. ERP System experience (e.g., Oracle) preferred.
IV. Work Environment/Conditions:
Plant: Standard automotive plant environment with moderate noise level. PPE (Personal Protective Equipment) such as safety glasses, steel toe shoes, hearing protection, etc. may be required in engineering, manufacturing, or industrial areas. Personal attire standards may apply.
Travel: Must be willing to travel up to 10% of the time.
V. Physical Demands:
While performing the duties of this job, the team member is required to talk, see, and hear. The team member must be capable of walking, sitting, and standing for extended periods of time and is occasionally required to lift up to 30 pounds.
Disclaimer: This job description is intended to identify the general nature and level of work performed by team members within this classification, as well as certain essential job functions. It is not intended, and should not be interpreted, as a comprehensive inventory of all duties, responsibilities, and qualifications required of team members assigned to this job. To qualify for this job, however, a team member must be able to perform its essential functions with or without reasonable accommodation. Under no circumstances may this job description be construed as altering the at-will nature of the employment relationship between TBA and any team member.