PROCESSING APPLICATION
Hold tight! We’re comparing your resume to the job requirements…
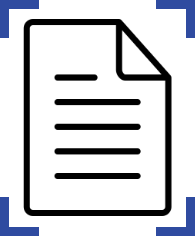
ARE YOU SURE YOU WANT TO APPLY TO THIS JOB?
Based on your Resume, it doesn't look like you meet the requirements from the employer. You can still apply if you think you’re a fit.
Job Requirements of Maintenance Supervisor/ Group Leader:
-
Employment Type:
Full-Time
-
Location:
Princeton, IN (Onsite)
Do you meet the requirements for this job?
Maintenance Supervisor/ Group Leader
-
General Summary:
Directs Team Leaders and other Team Members in assigned manufacturing area (e.g., assembly, filter, injection molding, powertrain, stamping, urethane, welding, kaizen, etc.) in the execution of the group’s responsibilities. Manages group (manufacturing line, cells, or area) as an operational unit and responsible to accomplish company goals and targets in accordance with all company policies, manufacturing standards and methods, and quality standards for safety, product quality, customer satisfaction, accuracy, productivity, cost reduction, housekeeping, efficiency, training, teamwork, and morale.
II. Essential Job Functions:
General
- Function as a first-line supervisor over team leaders and team members.
- Responsible for leading and maintaining the manufacturing and production system of assigned area, accomplishing department hoshin goals, and keeping on task with targets and implementation schedule.
- Utilize knowledge and skills to maintain the highest level of quality and efficiency possible.
- Lead continuous improvement activity for assigned area.
- Maintain a safe working environment for all team members.
- Train and coach team members to maintain productivity and quality standards, in TS19649, ISO 14001, environmental, safety, quality, job performance, setups, trouble shooting, and continuous improvement.
- Collect, record, and analyze information while maintaining documentation regarding the activities in the assigned area as defined by company policy, procedure, or practice.
- Communicate frequently with internal contacts on various issues.
Minimum Qualifications/Requirements:
Education:
- Associate’s degree in Business, Manufacturing, Engineering, or related field required, or an equivalent combination of education and experience. Bachelor’s degree preferred.
Experience:
- Minimum of three (3) years of relevant manufacturing experience required.
- Minimum two (2) years of previous leadership or supervisory experience required.
- Automotive industry experience preferred with parts production, quality, or production control experience a plus.
- Experience in automotive interiors including carpets, filters, powertrain, seating, and/or trim preferred.
- Working knowledge and experience with TPS and Production Efficiency (PEFF) system preferred.
Personal/Technical Skills:
- Demonstrated knowledge, skills, and abilities to perform the job functions of a leadership role.
- Must be able to work a fixed or rotating shift schedule, including daily or weekend overtime.
- Must be able to accept reassignment to any shift, assignment, or work location in the Plant.
- Thorough understanding of company product, trade terminology, quality management and control systems and techniques, manufacturing processes including material controls, work flow, scheduling, kanban, machine operation, and company policies as standards.
- Good mechanical aptitude.
- Basic math and analytical skills.
Language Skills:
- Strong verbal and written communication skills in English.
Computer/Software:
- Previous experience working with integrated computer programs and/or applications. ERP System experience (e.g., Oracle) preferred.
- Solid working knowledge and demonstrated experience with Microsoft Office and other computer-based applications (e.g., MS Word, MS Excel, MS PowerPoint, Outlook, Internet, etc.).
Training Requirements:
Must be willing to successfully complete and use training for items below as required by area of assignment:
- Forklift, tugger, and truck usage, and pass certification.
- Overhead crane operation.
- Cross training for leading other plant support departments.
- RCRA and DOT hazardous waste requirements, and pass certification.
- Computer-based software, applications, and systems (e.g., Oracle, Kronos, Future 3, etc.).
Work Environment/Conditions:
Office: Open Office Environment, moderate noise level.
Plant: Various types of manufacturing environments.
- Standard automotive plant environment with moderate noise level.
- PPE (Personal Protective Equipment) such as safety glasses, steel toe shoes, Kevlar sleeves, hearing protection, etc. may be required in designated engineering, manufacturing, or industrial areas. Personal attire standards may apply.
- Involves moderate or occasional presence of some slightly disagreeable conditions, i.e., cold, dust, heat, odor, etc.
Travel: Minimal
Physical Demands:
While performing the duties of this job, the team member is required to talk, hear, and see (with visual acuity). Performance requires mental alertness and sustained attention to needs of the department in terms of workflow, efficiency of operation, machine adjustment, and team member output. Performance requires physical ability to inspect, adjust, and operate equipment. The team member must be capable of walking, sitting, and standing for extended periods of time throughout plant. Occasionally climbing, stooping, or bending on, under, or near tooling and equipment. May be occasionally required to reach, grasp, and manipulate parts, materials, or equipment. May be occasionally required to lift up to 30-50 pounds (with or without assistance).
Disclaimer: This job description is intended to identify the general nature and level of work performed by team members within this classification, as well as certain essential job functions. It is not intended, and should not be interpreted, as a comprehensive inventory of all duties, responsibilities, and qualifications required of team members assigned to this job. To qualify for this job, however, a team member must be able to perform its essential functions with or without reasonable accommodation. Under no circumstances may this job description be construed as altering the at-will nature of the employment relationship between TBA and any team member.
EOE